Problem The intermediate shaft in the two-stage gearbox shown below is to be designed. The transmitted power is 100 kW through this shaft which is rotating at 2,500 rev/min. The dimensions are summarized in the table with variables corresponding to the figure. The gears have diameters d3 and d4, thicknesses tg3 and tg4, and both have a 20° pressure angle. The distance between bearings and gears are a, b and c. Input tos K = 2 g3 Input Shaft FE4 # ‒‒‒‒ → Intermediate Shaft Output Shaft k-tpt #10 Output Z d. d₂ a= b = C = d3 = tg3 = d₁ = tg4 = 350 200 250 300 50 200 50 mm mm mm mm mm mm mm Design the shaft with a minimum design factor of n = 4 for static yield and n = 1.5 for infinite life based on the Modified- Goodman criteria. Due to cost constraints, the mass of the shaft cannot exceed 25 kg (based on volume and density of the material you choose). The bearings and gears must be set against shoulders with steps of 1.2-1.5 D/d ratio, be fitted with appropriately size keyways (see Table 7-6), and all dimensions must be preferred sizes as listed in Table A-17 (you may use increments of 5 mm for sizes above 50 mm as well). Use the same bearing on both shaft ends, and reference Table 11-2 for basic bearing dimensions (diameter and width), ensuring that 3 times the "Cio" load rating for Deep Groove ball bearings is satisfied for the size you select Calculations showing the shaft passes both static failure and fatigue failure criteria for the specified design factor at multiple locations of potential high stress. Include a summary of the shaft mass. Be neat and clear in your methodology and results. Please provide some sample calculations and a results summary if you are submitting printed spreadsheet stress calculations. Make sure the spreadsheets are well labeled and easy to follow.
Problem The intermediate shaft in the two-stage gearbox shown below is to be designed. The transmitted power is 100 kW through this shaft which is rotating at 2,500 rev/min. The dimensions are summarized in the table with variables corresponding to the figure. The gears have diameters d3 and d4, thicknesses tg3 and tg4, and both have a 20° pressure angle. The distance between bearings and gears are a, b and c. Input tos K = 2 g3 Input Shaft FE4 # ‒‒‒‒ → Intermediate Shaft Output Shaft k-tpt #10 Output Z d. d₂ a= b = C = d3 = tg3 = d₁ = tg4 = 350 200 250 300 50 200 50 mm mm mm mm mm mm mm Design the shaft with a minimum design factor of n = 4 for static yield and n = 1.5 for infinite life based on the Modified- Goodman criteria. Due to cost constraints, the mass of the shaft cannot exceed 25 kg (based on volume and density of the material you choose). The bearings and gears must be set against shoulders with steps of 1.2-1.5 D/d ratio, be fitted with appropriately size keyways (see Table 7-6), and all dimensions must be preferred sizes as listed in Table A-17 (you may use increments of 5 mm for sizes above 50 mm as well). Use the same bearing on both shaft ends, and reference Table 11-2 for basic bearing dimensions (diameter and width), ensuring that 3 times the "Cio" load rating for Deep Groove ball bearings is satisfied for the size you select Calculations showing the shaft passes both static failure and fatigue failure criteria for the specified design factor at multiple locations of potential high stress. Include a summary of the shaft mass. Be neat and clear in your methodology and results. Please provide some sample calculations and a results summary if you are submitting printed spreadsheet stress calculations. Make sure the spreadsheets are well labeled and easy to follow.
Elements Of Electromagnetics
7th Edition
ISBN:9780190698614
Author:Sadiku, Matthew N. O.
Publisher:Sadiku, Matthew N. O.
ChapterMA: Math Assessment
Section: Chapter Questions
Problem 1.1MA
Related questions
Question
Please solve this using the second image to reference which dimensions to find to make it have the design factor and yield. And anything else necessary listed.

Transcribed Image Text:Problem
The intermediate shaft in the two-stage gearbox shown below is to be designed. The transmitted power is 100 kW through this
shaft which is rotating at 2,500 rev/min. The dimensions are summarized in the table with variables corresponding to the figure.
The gears have diameters d3 and d4, thicknesses tg3 and tg4, and both have a 20° pressure angle. The distance between bearings
and gears are a, b and c.
^y
Input
tb3
2
g3
b
tg4
Input Shaft
→
Intermediate
Shaft
Output
Shaft
K-tb4
Output
Z
4;
dz
3
a =
b =
C =
d3 =
tg3 =
d4 =
tg4 =
-
350
200
250
300
50
200
50
mm
mm
mm
mm
mm
mm
▬▬▬▬▬▬▬▬
mm
Design the shaft with a minimum design factor of n = 4 for static yield and n = 1.5 for infinite life based on the Modified-
Goodman criteria. Due to cost constraints, the mass of the shaft cannot exceed 25 kg (based on volume and density of the
material you choose). The bearings and gears must be set against shoulders with steps of 1.2-1.5 D/d ratio, be fitted with
appropriately size keyways (see Table 7-6), and all dimensions must be preferred sizes as listed in Table A-17 (you may use
increments of 5 mm for sizes above 50 mm as well). Use the same bearing on both shaft ends, and reference Table 11-2 for
basic bearing dimensions (diameter and width), ensuring that 3 times the "Cio" load rating for Deep Groove ball bearings is
satisfied for the size you select
Calculations showing the shaft passes both static failure and fatigue failure criteria for the specified design factor
at multiple locations of potential high stress. Include a summary of the shaft mass. Be neat and clear in your
methodology and results. Please provide some sample calculations and a results summary if you are submitting
printed spreadsheet stress calculations. Make sure the spreadsheets are well labeled and easy to follow.

Transcribed Image Text:ØXX
RXX
XX
X
Øxx
-XX
R XX
ØXX
RXX
XX
-XX X XX KEYWAY
ØXX
-XX
-XX
ØXX
RXX
-XX
-XXX XX KEYWAY
Øxx
RXX
XX
XX
Øxx
R XX
Expert Solution

This question has been solved!
Explore an expertly crafted, step-by-step solution for a thorough understanding of key concepts.
This is a popular solution!
Trending now
This is a popular solution!
Step by step
Solved in 7 steps with 24 images

Knowledge Booster
Learn more about
Need a deep-dive on the concept behind this application? Look no further. Learn more about this topic, mechanical-engineering and related others by exploring similar questions and additional content below.Recommended textbooks for you
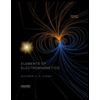
Elements Of Electromagnetics
Mechanical Engineering
ISBN:
9780190698614
Author:
Sadiku, Matthew N. O.
Publisher:
Oxford University Press
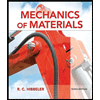
Mechanics of Materials (10th Edition)
Mechanical Engineering
ISBN:
9780134319650
Author:
Russell C. Hibbeler
Publisher:
PEARSON
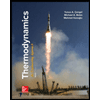
Thermodynamics: An Engineering Approach
Mechanical Engineering
ISBN:
9781259822674
Author:
Yunus A. Cengel Dr., Michael A. Boles
Publisher:
McGraw-Hill Education
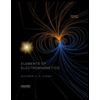
Elements Of Electromagnetics
Mechanical Engineering
ISBN:
9780190698614
Author:
Sadiku, Matthew N. O.
Publisher:
Oxford University Press
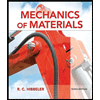
Mechanics of Materials (10th Edition)
Mechanical Engineering
ISBN:
9780134319650
Author:
Russell C. Hibbeler
Publisher:
PEARSON
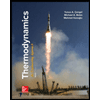
Thermodynamics: An Engineering Approach
Mechanical Engineering
ISBN:
9781259822674
Author:
Yunus A. Cengel Dr., Michael A. Boles
Publisher:
McGraw-Hill Education
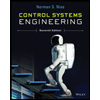
Control Systems Engineering
Mechanical Engineering
ISBN:
9781118170519
Author:
Norman S. Nise
Publisher:
WILEY
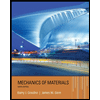
Mechanics of Materials (MindTap Course List)
Mechanical Engineering
ISBN:
9781337093347
Author:
Barry J. Goodno, James M. Gere
Publisher:
Cengage Learning
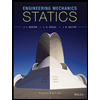
Engineering Mechanics: Statics
Mechanical Engineering
ISBN:
9781118807330
Author:
James L. Meriam, L. G. Kraige, J. N. Bolton
Publisher:
WILEY